Real-Time Data
Unlocking the Power of Real-Time Data
When we think about a process analyzer, it is easy to see it as just another piece of equipment. At Metrohm USA, we view it differently—it’s a powerful source of data. Our process analyzers give you real-time information that helps you optimize efficiency, ensure quality, and make informed decisions. From titration to spectroscopy, the data collected spans a broad spectrum of critical parameters, giving you a window into every stage of your production.
Curious about the impact our analyzers can have? Check out the examples below to see how our data-driven approach has improved processes and delivered measurable results for a wide range of industries.
![[2024] Graphs-Tighter Control-1 [2024] Graphs-Tighter Control-1](https://processanalytics.metrohmusa.com/hs-fs/hubfs/%5B2024%5D%20Graphs-Tighter%20Control-1.png?width=800&height=480&name=%5B2024%5D%20Graphs-Tighter%20Control-1.png)
Improving Control Through Process Monitoring
Maintaining tight control over effluent wastewater parameters is crucial across industries to avoid potential regulatory compliance issues. The graph illustrates how effective process monitoring and adjustments can lead to significant improvements in wastewater management. At first, the process is inconsistent due to infrequent grab sample monitoring, leading to delayed and reactionary adjustments.
With a process analyzer in place, proactive adjustments can be made using a data-centric approach. You can also have peace of mind knowing that if a process upset is detected, Metrohm’s analyzer will automatically activate a diversion valve, preventing the effluent wastewater from being discharged. This ensures compliance with environmental regulations around the clock.
Enhancing Process Efficiency Through Real-Time Monitoring
Boosting process efficiency can lead to significant gains across various industries. Traditionally, fermentation tanks are measured every 3-6 hours in an analytical lab. With NIR spectroscopy, this complex reaction can be monitored in real-time, providing data every hour, as illustrated in the graph.
![[2024] Graphs-Reaction Monitoring [2024] Graphs-Reaction Monitoring](https://processanalytics.metrohmusa.com/hs-fs/hubfs/%5B2024%5D%20Graphs-Reaction%20Monitoring.png?width=800&height=480&name=%5B2024%5D%20Graphs-Reaction%20Monitoring.png)
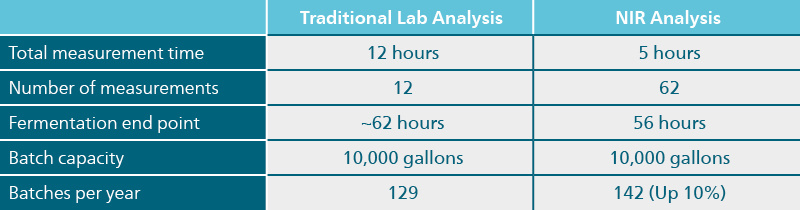
Shifting from traditional lab analysis to process analysis allows data collection to increase from 12 times per batch to an impressive 62 times. This higher frequency of data means the process can move to the next step as soon as the reaction is complete, reducing the fermentation step from around 62 hours to 56 hours. This improvement optimizes the process and increases plant capacity with just one instrument. As a result, batch production increased from 129 to 142 batches per year—a 10% increase.
Reducing Human Error with Process Analytics
Operators in the metal finishing industry often rely on hanging burettes or drop-test methods to perform titrations to maintain process control. These manual techniques introduce variations because each operator performs the tasks differently. Also, since there's no automated reporting, the results can't be easily traced back for quality assurance, leading to variability and potential quality issues, as shown in the first graph.
The second graph tells a different story. Introducing a process analyzer stabilizes process control. The analyzer continuously monitors the process, providing real-time data to a DCS/SCADA or LIMS for accurate bath control. With Metrohm’s process analyzers, operators no longer need to adjust the bath manually. These analyzers can activate pumps to dose chemicals properly into the bath, maintaining consistent bath quality. This automated dosing ensures precise chemical control, chemical cost savings and optimal process control, all while keeping the desired parameter within a tighter range.