ROI
Sustainable Building, Profitable Outcomes
Each block you add with Metrohm supports sustainability and enhances your return on investment. See how reducing waste and optimizing operations can contribute to environmental goals and substantial economic benefits.
The Path to Faster, Cost-Effective Fuel Testing
Conventional fuel sample analysis for key parameters like research octane number (RON), motor octane number (MON), and aromatic content is a multi-step process that can be both time-intensive and costly. This traditional approach involves sample preparation, separate analyses using distinct ASTM methods (D2699 for RON, D2700 for MON, and D5769 for aromatics), and subsequent cleanup procedures before the next batch can be processed. This methodology presents significant challenges regarding throughput, resource allocation, and operational expenses for laboratories handling thousands of samples annually.
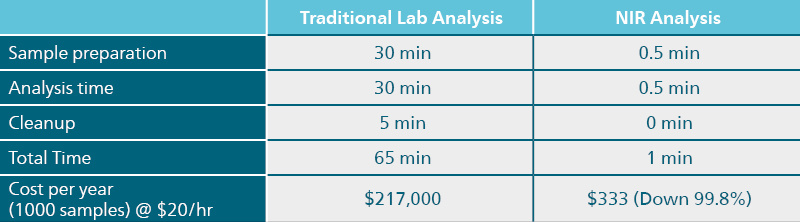
Inline near-infrared (NIR) spectroscopy offers an approach to fuel analysis that dramatically streamlines the process. This method minimizes sample preparation, eliminates the need for extensive cleanup procedures, and delivers results almost instantaneously. By providing comprehensive data in just minutes, NIR spectroscopy significantly reduces analysis time compared to traditional methods. The efficiency gains translate directly into operational cost savings. Moreover, the rapid turnaround allows for higher sample throughput, optimizing laboratory resources and personnel time.
Protecting Membranes and Profits in Chlor-Alkali Operations
Hardness breakthrough presents a significant challenge in chlor-alkali production. Elevated calcium and magnesium levels can lead to scale formation, clogging membrane pores and structural damage. This degradation impairs membrane efficiency, driving up power consumption and compromising product quality. Even slight excursions in brine purification can result in a loss of membrane efficiency, sometimes up to 10% in four hours. The risk escalates when hardness breakthrough goes undetected, potentially necessitating costly premature membrane replacement across multiple electrolytic cells. Given the high cost of these membranes and their crucial role in production, maintaining optimal brine quality through rigorous monitoring and purification is essential for operational efficiency and cost-effectiveness in chlor-alkali plants.
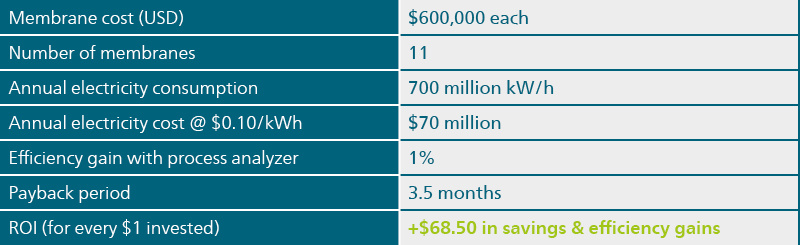
Online process analyzers provide a significant cost advantage by protecting valuable membrane assets and boosting efficiency. Enhancing the brine purification process with these analyzers can deliver substantial savings—even a modest 1% efficiency gain can make a notable impact, especially with annual electricity costs reaching $70 million. Beyond monitoring hardness levels with traditional photometric methods, online ion chromatography can be used to detect strontium, a calcium and magnesium hardness precursor. This early detection capability helps prevent potential issues, ensuring membranes are safeguarded, and the purification process remains optimized. The rapid ROI underscores the importance of continuous, real-time monitoring in preventing costly membrane damage and maintaining peak operational performance.
Ensuring Quality and Yield Through UPW Monitoring
Ultrapure water (UPW) is the most consumed chemical in semiconductor fabrication, with some plants using up to 15 million liters per day. UPW is critical for rinsing after etching steps and diluting concentrated chemicals. Even trace impurities in UPW can lead to uneven etching or plating, modifying the electrical properties of silicon wafers and causing defects in the final integrated circuits. Given the high stakes, even a slight drop in yield can result in significant financial losses, making rigorous UPW monitoring essential for operational success.
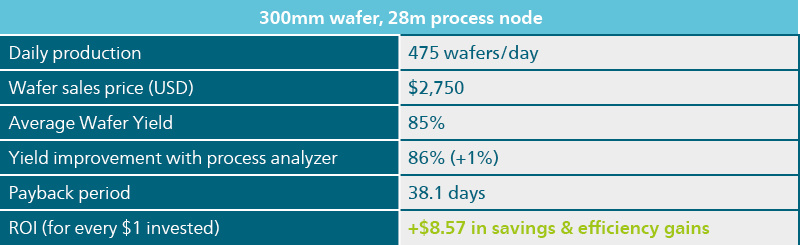
Online ion chromatography (IC) provides a novel advantage by detecting trace anions, cations, and silica contaminants in UPW in real-time. This allows for immediate process adjustments to maintain optimal water quality. As shown in the ROI table, a 1% increase in wafer yield for a 300mm fab running a 28nm process node can translate to over $8.50 in savings and efficiency gains for every $1 invested in a process analyzer. With a payback period of just 38 days, the benefits of online UPW monitoring with IC are clear. Improved process control and reduced defects lead to higher quality chips and a faster return on investment.